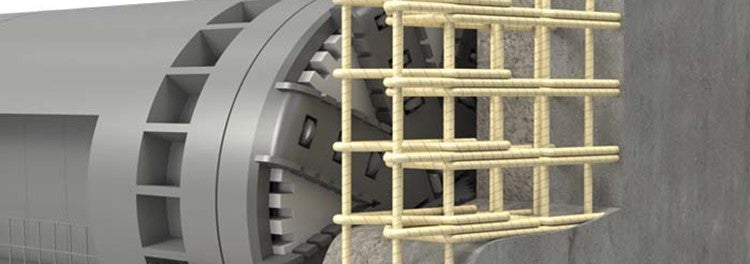
Key Information
InfraBuild is delivering the Melbourne Metro Tunnel Project with its supply and installation of Dextra ASTEC Soft-Eyes D-Wall cages.
Tunnelling is set to begin on the twin 9km tunnels of Melbourne’s Metro Tunnel Project now that the first of four tunnel boring machines (TBM) has been delivered to site.
According to Metro Tunnel, “the enormous machines will support a crew of 14 workers, including a pilot directing the TBM on its journey through Melbourne’s underground.
“Each is manned 24 hours a day, 7 days a week as they bore through hard rock and sand at a speed of around 10 metres per day.”
Work has already begun on the excavation and construction of five new underground stations – Parkville, State Library, Town Hall stations, North Melbourne and Anzac stations – with two construction methods used to deliver the stations.

Excavation methods
Trinocular excavation involves the mining of three overlapping tunnels by roadheaders to create a wide, open space that allows station concourse and platforms to be integrated on a single level. Cut and Cover involves the use of excavation equipment to dig a large trench or rectangular hole in the ground, which is then covered by a concrete deck. This enables the resumption of surface construction activity while construction works continue below. Concrete panels are then used to form the various levels and internal structures, similar to the construction of the underground basements of high-rise buildings
The Parkville, North Melbourne and Anzac stations will be constructed using the Cut and Cover method. Each will require the excavation and construction of a void up to 100m long and 30m wide. Prior to excavation, diaphragm wall (D-Wall) cages are installed to create a perimeter cage for the station void.
GFRP D-Walls
Up to 250 steel reinforcement cages will be installed in each station. Within these D-Walls, Dextra’s ASTEC Soft-Eyes, made of Glass Fibre Reinforced Polymer (GFRP), are inserted as an advantageous replacement for conventional steel rebars. These lightweight, fully corrosion-resistant and high-tensile performance rebar cages allow the TBM to break through the diaphragm walls and secant piles without inflicting damage to either, eliminating the complex and potentially hazardous task of removing steel reinforcement and rapidly connecting the rail tunnels and stations.

Developed by Dextra in 1996, the Soft-Eye technology was first used on Bangkok’s MRT subway stations. Dextra’s Regional Sales Manager, Karsten Doering, said: “Thanks to the design of the ASTEC GFRP Soft-Eyes, the TBM simply breaks through the station’s D-Wall by cutting the GFRP reinforcement and crushing the concrete. This method is the fastest, simplest and safest way to create tunnel openings.
“The close and effective collaboration between InfraBuild Construction Solutions (formerly LIBERTY OneSteel Reinforcing), Dextra and the KIJV site team allowed design, custom-made production of the GFRP bars and hooks, delivery to the assembly facility (including airfreight, for instance), and pre-fabrication of rebar cages, including the ASTEC Soft-Eyes to meet the project’s tight construction schedule,” Karsten said.
“This is a great example of a fully integrated value chain benefiting the contractor’s bottom line. At Dextra we are looking forward to participate in more projects following this good example.”

InfraBuild Construction Solutions’ Micah Biggs is managing the project to funnel a daily supply of up to 150 tonnes of fabricated cages to the Melbourne Metro Tunnel Project.

“The steel reinforcement D-Wall cages are constructed from Australian-manufactured InfraBuild steel in our Derrimut processing facility,” he said. “We also supply and insert the GFRP Dextra ASTEC Soft-Eyes as required and deliver progressively to the construction sites to enable the project to continue on schedule.”

Related Case Studies
Subscribe to the
InfraBuild newsletter
Receive regular updates on news, case studies as well as the latest products and services.