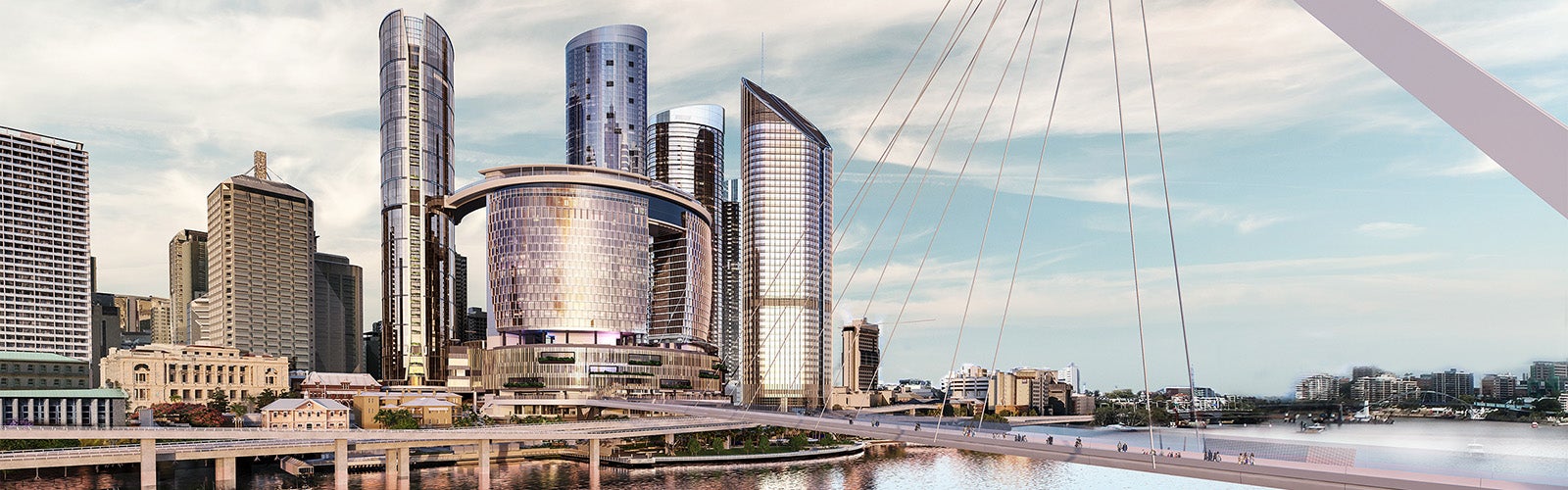
Key Information
- InfraBuild Reinforcing will supply at least 12,500 tonnes of reinforcing steel to the city-shaping project
- The company’s integrated supply chain has allowed it to accelerate supply of reinforcing steel to meet the project’s needs
- Two raft slabs have been poured ahead of schedule for the project’s four towers
InfraBuild has been closely involved in foundation works for Brisbane CBD’s newest precinct, the largest construction project currently underway in Queensland.

InfraBuild has kept the Queen’s Wharf project ahead of program by accelerating its supply of reinforcing steel to site for two of the project’s large raft slabs.
Approximately 700 tonnes of reinforcing has been used in the two slabs, which form a base for two of the four towers that will make up Brisbane’s $3.6bn Queen’s Wharf Brisbane Integrated Resort Development.
Michael Jostsons, InfraBuild Reinforcing Project Manager, says the schedule for supply and delivery of cut and bent bar for the slabs originally allowed for a 14-day period between each. However, the business was able to meet the Principal Contractor’s request to supply both simultaneously. The solution has helped Multiplex continue to deliver the program ahead of schedule.
“We committed to a supply program from the outset and we exceeded expectations by increasing the supply when requested,” Michael says.
“We were effectively asked to double-up on our supply,” he says. “It put the pressure on, but we were glad we could exceed our original commitment.”
Benefits of vertically integrated supply
The supply of steel for the raft slabs is one component of InfraBuild’s total supply package, which will amount to more than 12,500 tonnes by project end. The bulk so far has been cut and bent heavy bar (up to 40mm), plus mesh, both of which come from InfraBuild Reinforcing’s Acacia Ridge facility on Brisbane’s southside.

Managing that volume of reinforcing steel from the production facility for use in the raft slabs, each of which is up to 2.2m deep, required coordinated forward planning. The slabs had up to 17 layers of reinforcing and at peaks in the delivery program InfraBuild Reinforcing was delivering up to 90 tonnes per day.
“Given that it was heavy bar, relatively limited supply is held in stock,” Michael explains. “We had to work with the mill to plan availability of stock so we could process the bar, schedule it and get it out to site.”
It’s one of the advantages of InfraBuilds’ vertically integrated supply chain that it can collaborate with upstream production facilities when required and scale up its ability to process large volumes of bar at its manufacturing facilities on demand.
Delivering to a large project site in the CBD has added challenges.
“Queen’s Wharf is currently the largest construction project underway in Queensland—and it’s in one of the busiest parts of the Brisbane CBD,” says Michael. “We’ve successfully cooperated with other trades, suppliers and materials going in and out on a restricted delivery pattern; and we’ve needed to coordinate with multiple cranes and unloading areas within the site.

“There are currently nine towers on site—with the tenth expected in 2020 — which is about as many as I have ever seen on a site at the one time. That’s where the complexity in this project lies.”
He says projects the size of Queen’s Wharf reinforce the need for close collaboration between suppliers and the principal contractor – in this case, Multiplex.
“These projects are all about forward planning and having flexibility to meet program needs,”Michael says. “What’s important is good communication and making sure there’s a conduit between our business and theirs to resolve challenges together.”

Iconic project for Brisbane
Design of the Queen’s Wharf Development has been led by Cottee Parker Architects, which forms part of the Destination Brisbane Consortium chosen by the Queensland government to transform the site. Multiplex has been contracted to deliver the project’s shell and core works, including the basement, base services, the tower structures and the façade of the main integrated resort.
As at September 2019, Multiplex had overseen the pouring of the first section of suspended basement. What was a 26m-deep hole below George Street will soon be five levels of basement, the largest in the Brisbane CBD.
The Brisbane city skyline will be radically altered by the time Queen’s Wharf’s sculpted towers are complete. The new precinct will comprise four new luxury hotels, 2000 residential apartments, more than 50 new bars and restaurants, a riverfront moonlight cinema and offer more than 12 football fields of public space. An elevated Skydeck that takes inspiration from the verandah of traditional ‘Queenslander’ houses will be publicly accessible and offer 360-degree views of the river, the city and its surrounds.
A new casino, which replaces the existing Treasury Casino, will operate in the arc-shaped building facing the Brisbane River, with the existing Treasury Casino building on nearby William Street set to close its doors and reopen as a high-end boutique retail centre. A footbridge will connect the site with Brisbane’s Southbank on the opposing side of the river.
So large is the new precinct that it will occupy approximately 10 per cent (27.312 hectares) of the area of the Brisbane CBD.
Images courtesy Destination Brisbane Consortium
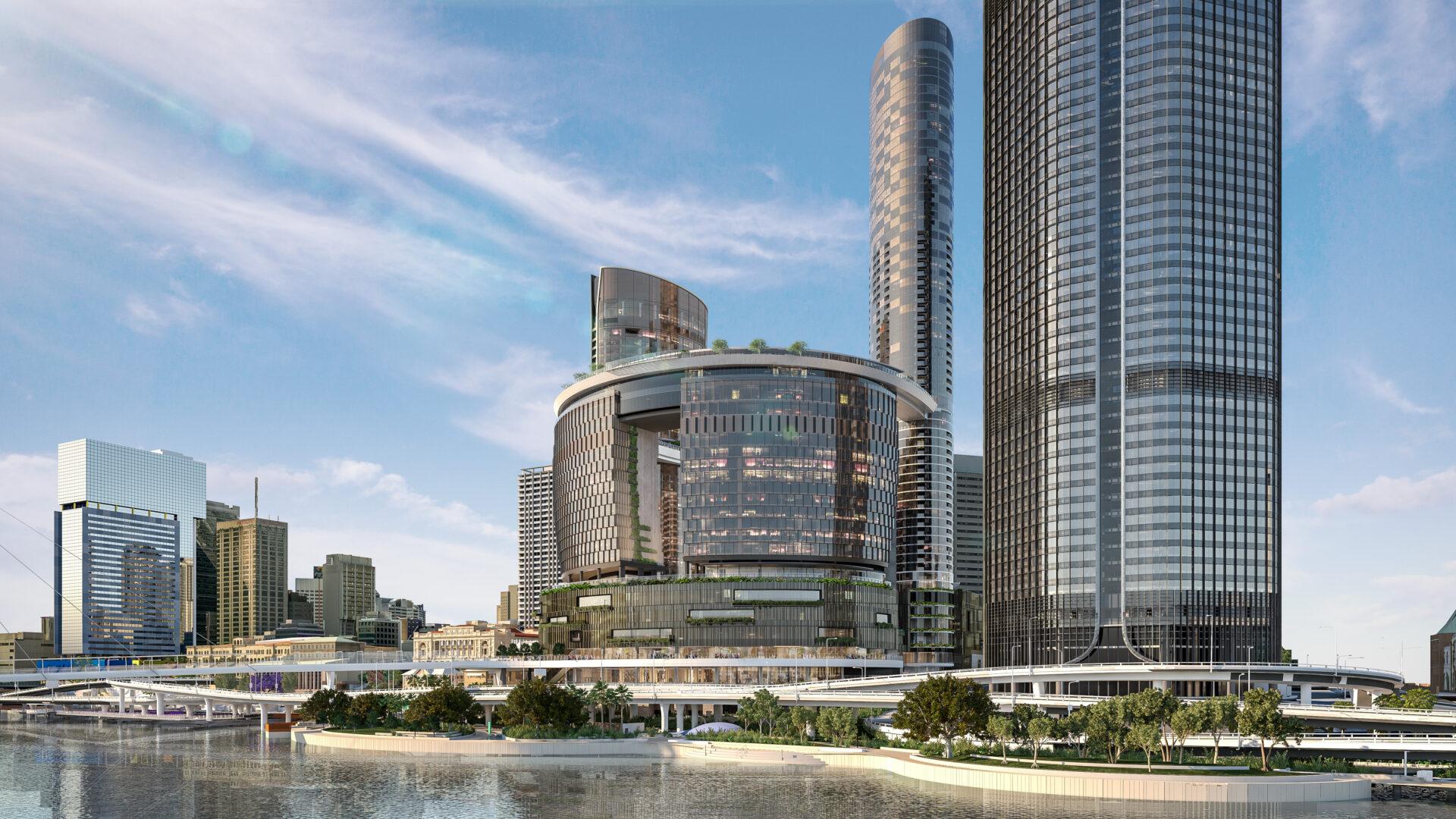
Related Case Studies
Subscribe to the
InfraBuild newsletter
Receive regular updates on news, case studies as well as the latest products and services.