Home / Our Stories /
Continuous Improvement: Teamwork powers up successful transformer installation
3 February 2022
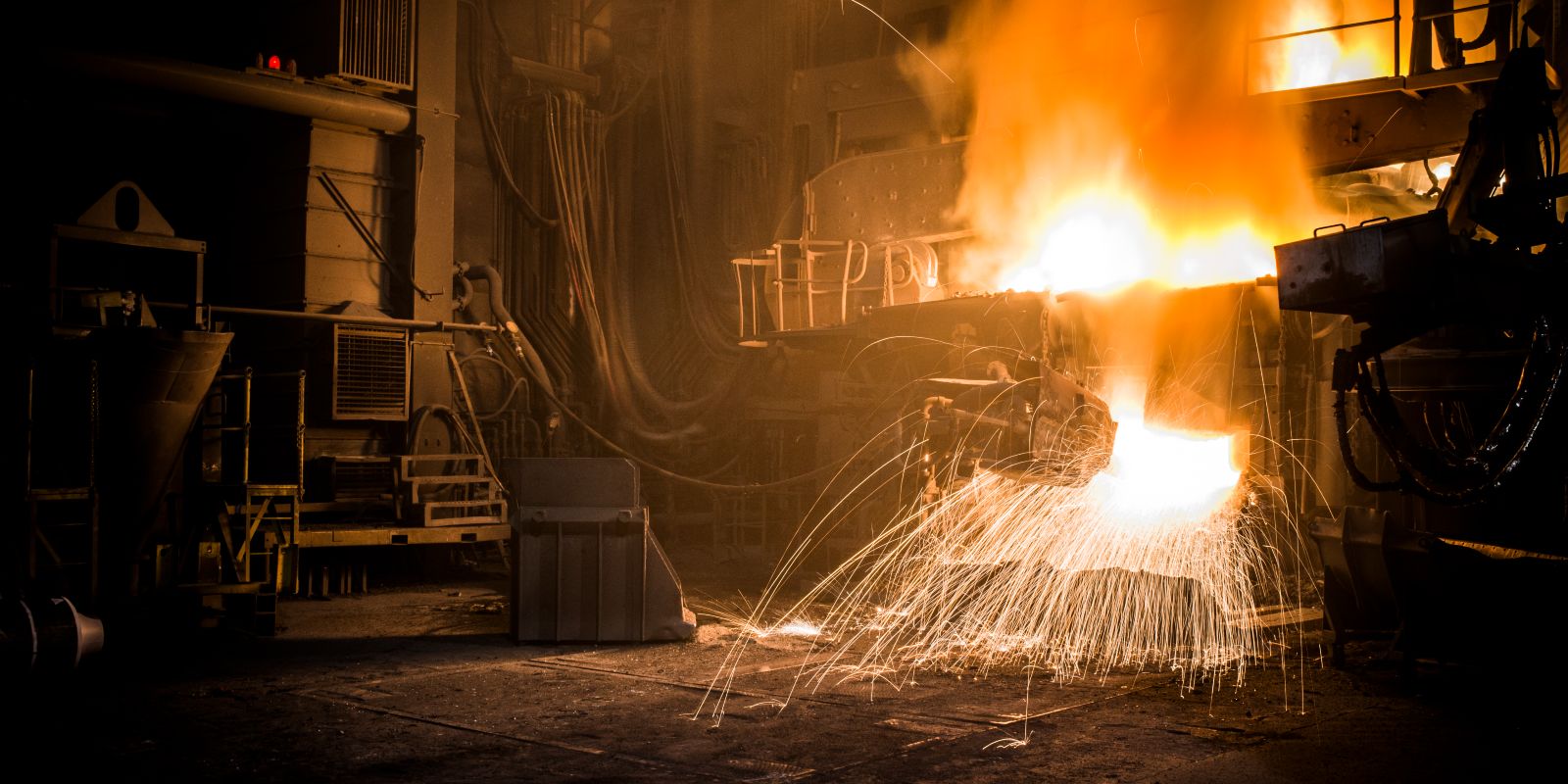
Two Electric Arc Furnaces (EAF) located at InfraBuild’s manufacturing sites in Sydney and Laverton are at the core of these steelmaking facilities. The seamless functioning of both EAFs is critical to operations and ensures InfraBuild customers are always supplied with quality steel products.
Due to the critical nature of the EAFs, the installation of a new transformer has seen a major operational security risk eliminated at the Sydney Steel Mill.
During the Christmas/New Year shutdown at Sydney Steel Mill, the main transformer (TX1), which supplies power to the EAF transformer was upgraded. With the transformer’s installation, the active power input into the Sydney EAF has increased from 56.2 MW to 61.5 MW. In production terms, this is an increase in billet production of around 45,000 tonnes per year.
Multiple, significant long-term benefits to InfraBuild include lower costs, increased self-sufficiency and a lower carbon footprint achieved through making our own rather than sourcing billet externally.
“By purchasing and installing a new, higher power No.1 transformer, the operational risk of an unplanned outage and having to operate at reduced capacity has been eliminated,” explained the Project’s Coordinator, Gilbert Du.
“Replacement of the No.1 transformer before failure has provided the site with a spare transformer sized for present operations and also provided us with a dedicated spare for the No.2 transformer,” Gilbert said.
The main transformer’s installation was a large complex project requiring a team of people with highly specialised skills across a variety of engineering disciplines. The team required experience with heavy rigging, fit-up, cabling, isolation, instrumentation and PLC’s (programmable logic control).
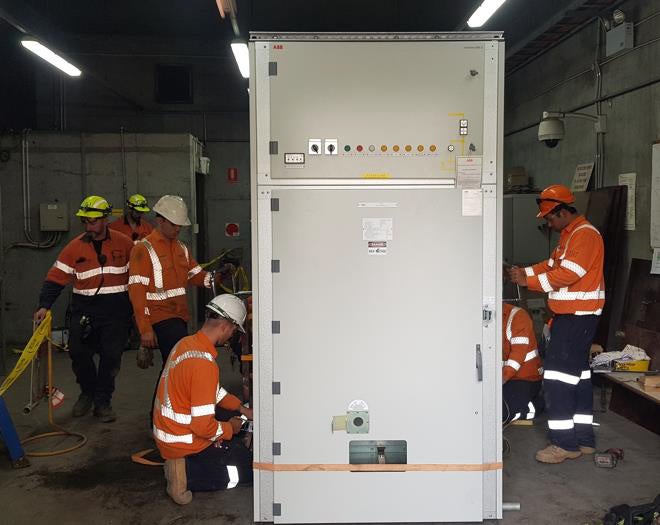
Along with the transformer change-out, the capacity of the high voltage switchgear was upgraded with improved safety features to handle increased loads (cabling, earthing, switchboard, protection panel and switches).
The successful installation of the transformer was largely thanks to the hard work and ingenuity of the Sydney Melt shop maintenance and engineering teams.
One of the most challenging aspects of the project was the late delivery of several essential components. The project team managed the delays well with parts air freighted to meet the installation deadline. The delivery of the disconnector switches, the HV Panel and the circuit breaker – manufactured in China, Italy and Germany, were all affected by COVID and difficult supply chains.
“It was ‘touch and go’ whether some of this gear would arrive in time and the team had to change plans a few times to cope with changing delivery dates,” said InfraBuild’s NSW Head of Rod and Bar Manufacturing, Steve Elliott.
“It was a combined stellar effort,” Gilbert said. “The project team was able to navigate through multiple technical and logistical challenges and managed to complete the installation on time with a shortened shutdown timeframe.”
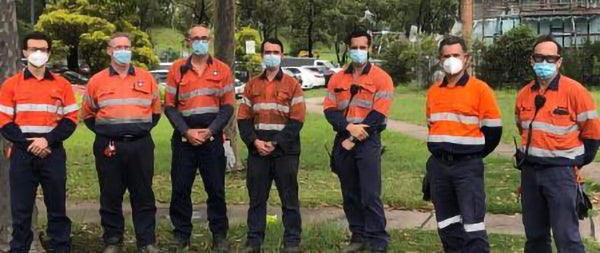
The electricity which feeds the Sydney Steelworks is supplied at high voltage (132kV) and is stepped down, in two stages via large transformers, to the operating voltage of the EAF.
Condition monitoring on the primary step-down transformer (TX1) showed it was approaching the end of its expected service life (30+yrs). The failure of the transformer without a spare would’ve led to unacceptable business impacts. The secondary transformer (the ‘engine’ of the EAF) was upgraded a couple of years ago from 72MVA to 90MVA. However, the full benefit of this upgrade couldn’t be realised until now due to the limited capacity and age of the TX1 transformer.
Following the successful start-up after the shutdown, a ramp-up of production from the EAF is now underway.
Please contact us for any feedback or media enquiries about this content.
Subscribe to the
InfraBuild newsletter
Receive regular updates on news, case studies as well as the latest products and services.