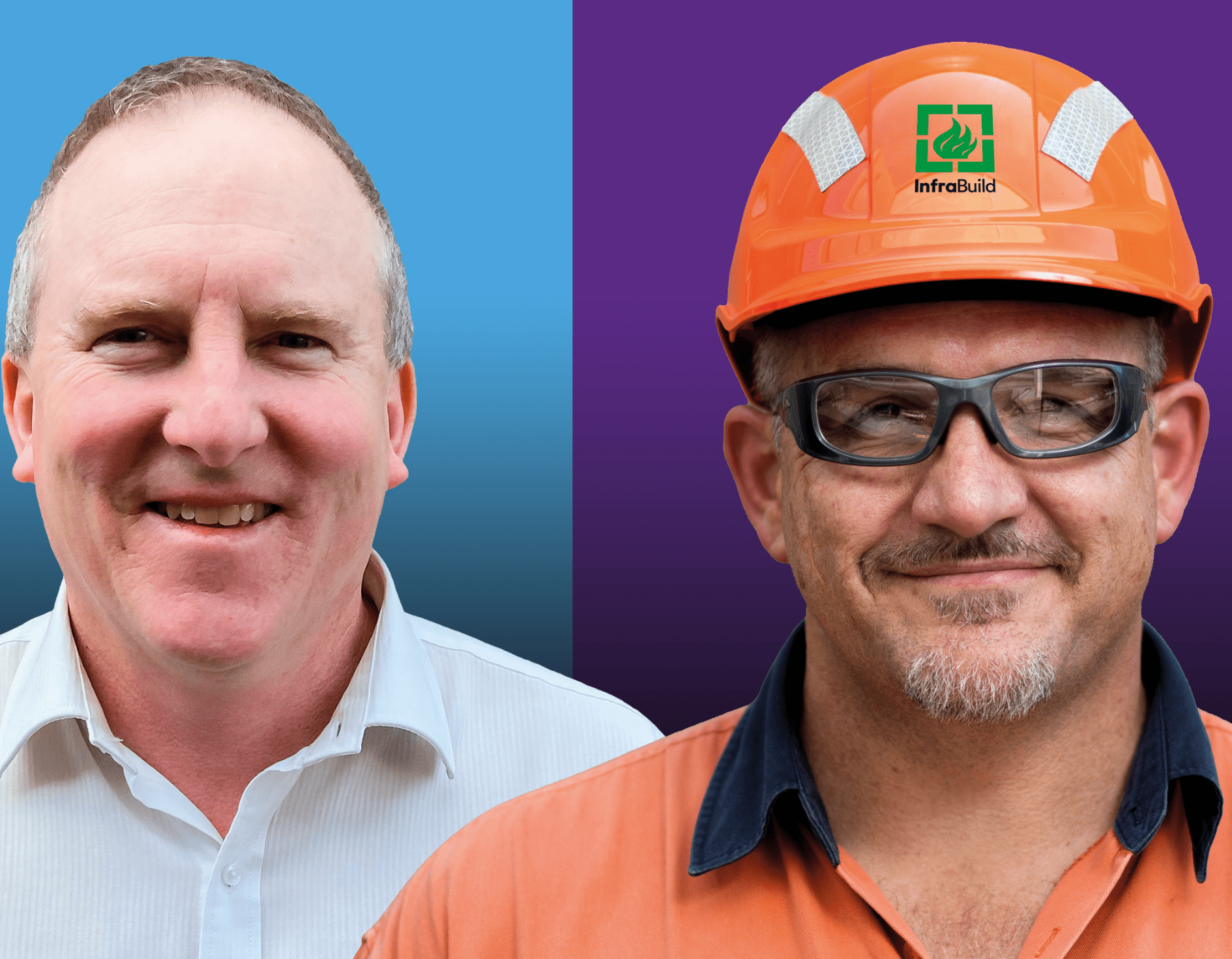
InfraBuild has rod and bar manufacturing operations in New South Wales (Rooty Hill and Newcastle) and Victoria (Laverton).
We recently sat down with Stephen Elliott (pictured left), Head of NSW Rod and Bar Manufacturing and Hercules Van der Merwe (pictured right), Head of VIC Rod and Bar Manufacturing to understand what happens there, and why our ‘we are stronger when we work together’ value is so important to our Rod and Bar teams.
Q: Tell us about your mills?
Hercules: Here in the Garden state, Laverton operations began in 1980, but our site was first just a Meltshop. The “Melt” bit is our Electric Arc Furnace (EAF) which we use to melt down recycled scrap metal and the first stage of our vertically-integrated manufacturing process. In 1984, we added the Laverton Bar Mill and the Rod Mill in 1996. Now we are the workplace to 406 employees.
Stephen: At Laverton they have everything on one site, but in New South Wales we are a little different. We have operations split across Rooty Hill and Newcastle. In Rooty Hill we have a Meltshop and Bar Mill, while our Newcastle site is home to a Rod Mill, Contistretch and Distribution Centre. We are celebrating the Newcastle Rod Mill’s 60th birthday later this year, which is pretty cool.
Q: What’s something interesting about your mills?
Stephen: The combined capacity of the two NSW Mills is the largest with a capacity of nearly 1.25Mtpa and we have the larger product ranges. Also, our Newcastle Rod Mill is a two strand Mill, which means we can roll two billets simultaneously (side by side).
This means our Newcastle site can roll the most billets compared to anywhere else in our business and even has the capability of rolling high carbon rod for InfraBuild Wire.
Hercules: At the Laverton site, we are the biggest single consumer of recycled scrap metal in Australia, which we are very proud of as it is in line with our focus on sustainable steel.
Q: What does sustainable steel mean to you and your operations?
Hercules: We are Australia’s only fully vertically-integrated steel manufacturer spanning scrap metal recycling, steel manufacturing and downstream distribution – this is something we are really proud of.
Stephen: Both the Rooty Hill and Laverton Electric Arc Furnaces use recycled scrap metal to manufacture steel products with lower levels of embodied carbon, compared to those made by traditional steelmaking methods.
Hercules: Recycling scrap metal drives material circularity, reduces emissions, saves on natural resources and diverts scrap from landfill.
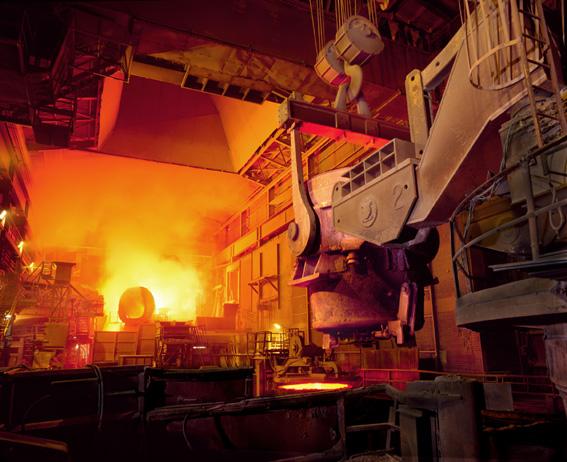
Q: How big are the furnaces?
Stephen: The Sydney furnace can hold up to 100 tonnes of liquid steel but the size of a heat or batch is usually 85 tonnes.
Hercules: The Laverton EAF capacity is the same as that of Sydney.
Q: Tell us more about the steelmaking process?
Hercules: The process starts the same. You get your scrap, melt it in the Electric Arc Furnace and then we pour it into a big ladle. The ladle then goes to the ladle furnace at a temperature of around 1640°. Inside the ladle furnace we can adjust the temperature and chemistry of steel to get it just right for casting.
We can use just about any scrap metal, as long as the major part of it is ferrous – that is, metal that contains iron. Laverton recently melted all of the railway cars that have been recently scrapped in Melbourne!
Stephen: When you cast steel, it turns from a liquid to solid. We make long lengths of steel with a square cross section and these are known as billets. In NSW, our billet weight is 1.5 tonnes, but in VIC, theirs is 2.2 tonnes. The billets are either warm (ideally) or cold charged into the Bar Mill or sent via road to the Newcastle Rod Mill. This is where having everything on one site benefits Victoria a little, as there is less movement.
Q: What happens in the Rolling Mill?
Stephen: It goes back into the natural gas fired reheat furnace – the steel gets hot and softer, not a full melt and it’s in the Rolling Mill we can change the shape, temperature and mechanical properties of the metal.
Once cool, we cut it to the length required. The lengths can range from 6 metres to 18 metres. We can make over 220 different steel products including reinforcing bar, flat bar and angles.
Q: And then the Rod Mill?
Hercules: At the Rod Mill we make coils. One billet equals one coil, so the bigger the billet, the bigger the coil. Coil can be used in a range of industrial applications such as engineered and reinforcing concrete structures, where mesh and bar – supplied by our downstream businesses – are used.
Q: With so many people on-site, operating such big and complex machines, safety is a concern. How do you put safety first?
Hercules: We have done a lot of work in this area; not just physical safety, but psychological safety and mental health – particularly given Victoria’s lengthy lockdown during COVID.
Stephen: Yes, it’s important for us all to keep up the effort in this area. All too often, workplace injuries happen when the mind is elsewhere; a fight with your partner at home, stress, mental health issues – all these things can be distracting and when your head isn’t in the game you can put yourself or your teammates at risk. The steel industry has significant hazards and injuries can easily become fatalities, so we put a lot of effort into both safety controls and mental health – looking out for one another is just as important as safety controls like lockout systems, exclusion zones and engineered barriers.
Hercules: We have many team members who are passionate about mental health and are active in the mental health space. We have set up a private room on-site for people to go and just talk – if they need some space to take a second out of their day.
Q: How do you work together?
Hercules: We make the same products, but service different regions which means our footprint across Australia is broad. However, our teams are connected in both states so we can swap ideas, resolve challenges quicker and more comprehensively through our established “Best Practice Network”.
Stephen: Absolutely – it’s one of the biggest strengths in our business. Around 2018-2019, the Sydney Meltshop had two High Voltage Transformer issues. The Laverton crew, who have some very experienced team members, came up immediately to provide their advice and expertise. This was invaluable and got us moving again.
Our mills and the teams that work in them are proud of their history and their role in helping InfraBuild deliver on its commitment to build futures through sustainable steel.
Please contact us for any feedback or media enquiries about this content.
Subscribe to the
InfraBuild newsletter
Receive regular updates on news, case studies as well as the latest products and services.